Precision Grinding Alternatives for Superfinishing, Lapping, and Honing
Achieve Honing, Lapping, and Superfinishing-Like Results With Duval Precision Grinding
For many OEMs, precision grinding is a highly effective and time-saving process that can also be the quickest method to achieve your required surface finish. When surface finish tolerance requirements are tight and conventional rough grinding methods will not suffice, our grinding experts utilize advanced precision grinding methods as a cost-effective means to replicate the desired outcomes without the need for secondary operations. If you are looking to upgrade your current finishing process, precision grinding may be the easiest, fastest, and most cost-effective way to get your surface finish to spec.
Is Precision Grinding A Viable Alternative to Superfinishing, Lapping, or Honing?
Superfinishing, lapping, and honing are three refinement methods used to achieve a specific surface finish or refine the geometry of precision components. Although the three processes are similar, each has a unique methodology, execution, and result.
Honing and Honing Alternatives
Honing is a high-precision process used to improve form characteristics such as cylindricity and surface finish. Honing is used to improve the geometry of a part, adjust the alignment of features such as holes or bores, and, in some cases, produce a specific surface finish on the interior bore. In instances where a cross-hatched microfinish is not required, precision ID grinding executed by a skilled professional can produce nearly identical results while eliminating the need for costly secondary operations.
Lapping and Lapping Alternatives
Lapping is a machining process used to achieve surface flatness on parts that require accuracy at the microscopic level. The lapping process involves passing a part between one or two large flat-lap plates or platens in a carrier fluid containing an abrasive. Duval achieves a flat, polished surface by applying precision surface grinding methods that exceed the flatness of typical rough grinding, usually generating surface flatness within .0002 – .00005”.
Superfinishing and Superfinishing Alternatives
Superfinishing is used to refine a component, producing a crosshatched surface finish with an exceptionally low roughness average (RA), typically below 8 µin. Superfinishing can increase the life of a part by decreasing wear and tear. It can also be applied to achieve a tighter tolerance and better sealing capabilities. While conventional rough grinding processes can generally achieve approximately 16 µin, our expert precision grinders can often achieve outcomes close to 5 µin or lower through precision grinding methods.
Eliminate Unnecessary Secondary Operations With Superfinishing, Lapping, and Honing Alternatives
The experts at Duval Precision Grinding understand that the precision components they produce play a vital role in some of the world’s most advanced equipment. These high-powered machines need robust, reliable, high-quality parts, and our precision grinding services deliver just that.
When we say precision is our only product, we mean it. Our commitment to precision grinding innovation led us to develop several methods that produce exceptional results while reducing overall production time and cost. Contact the experts at Duval today to discuss how superfinishing alternatives can help you streamline your production process.
How to Choose A Precision Grinding Vendor
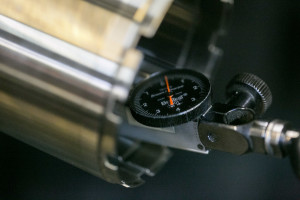
Expertly executed inspections and quality checks throughout the grinding process ensure parts satisfy all expectations.
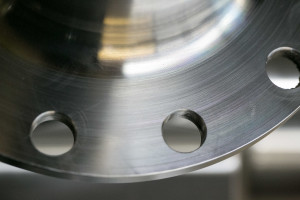
Duval’s precision grinding services can bring parts to spec without the need for costly secondary finishing operations.