Turbine and Jet Engine Seal Grinding
Turbine and Jet Engine Seal Grinding
Engine seals are some of the most challenging parts to grind due to their large size, unique shape, necessary tolerances, and handling requirements. Before the engine seal reaches the grinding stage of production, it is typically treated with a plasma coating, hardening treatment, abradable coating, and/or shot peening.
Turbine engines generally feature multiple seals that work cooperatively to regulate a multitude of factors, including:
- Gas flow
- Thermal regulation
- Pressurization and venting
- Thrust balancing
The stresses and the seal clearances these components face will vary depending on the engine condition; engine conditions while idling, climbing, or taking off will have different effects on the engine seal components.
Tight Tolerances and Difficult Coatings are No Problem
Because these seals are involved in critical processes such as gas flow or temperature regulation, the grinders working on them must be able to hold very precise tolerances to achieve the desired results. The coatings and treatments applied to engine seals tend to be hard and brittle, so grinding operations and handling must be done with the utmost care to avoid chipping, scratching, or cracking. Proper handling and grinding techniques ensure the integrity of the coating and reduce the likelihood of damage during transport.
Our grinders bring a wealth of experience in grinding complex components for a variety of seal types including labyrinth seals, honeycomb seals, and knife-edge seals. This familiarity with the challenges and specialized handling requirements of engine seals ensures your parts will be treated with the utmost care to return reliable, high-quality finished components.
Some seal features utilize an abradable coating, which wears as the part rotates to create a precisely fitted seal. This kind of coating requires grinding operations to fit the part correctly; tight tolerances mean an experienced hand must avoid grinding the material too aggressively. Improper handling can lead to the distortion of thin parts. For example, ID grinding the walls of a honeycomb seal can twist or warp the material if too much torque is applied. This will impact usability of the seal and potentially render the part useless.
Precision Grinding Services That Meet Your Deadlines
Grinding is usually the last process before the part is delivered to the customer. This means two things: First, turnaround time is tight. Second, the part is high-risk because the grinder is now entrusted with a part that is already worth quite a bit in material and labor. Any mistakes at this stage of the process can be tremendously expensive.
Our team of grinding experts has years of experience in grinding and finishing challenging parts. Duval Precision Grinding has sustained its reputation for excellence by always doing what it takes to return a good part. When it comes to engine seals, our grinders will ensure that you receive a perfectly finished piece on time, every time.
Do you have a turbine engine seal that needs the expert touch for grinding and surface finishing? Contact the experts at Duval Precision Grinding today!
Experts on Grinding Turbine & Jet Engine Seals
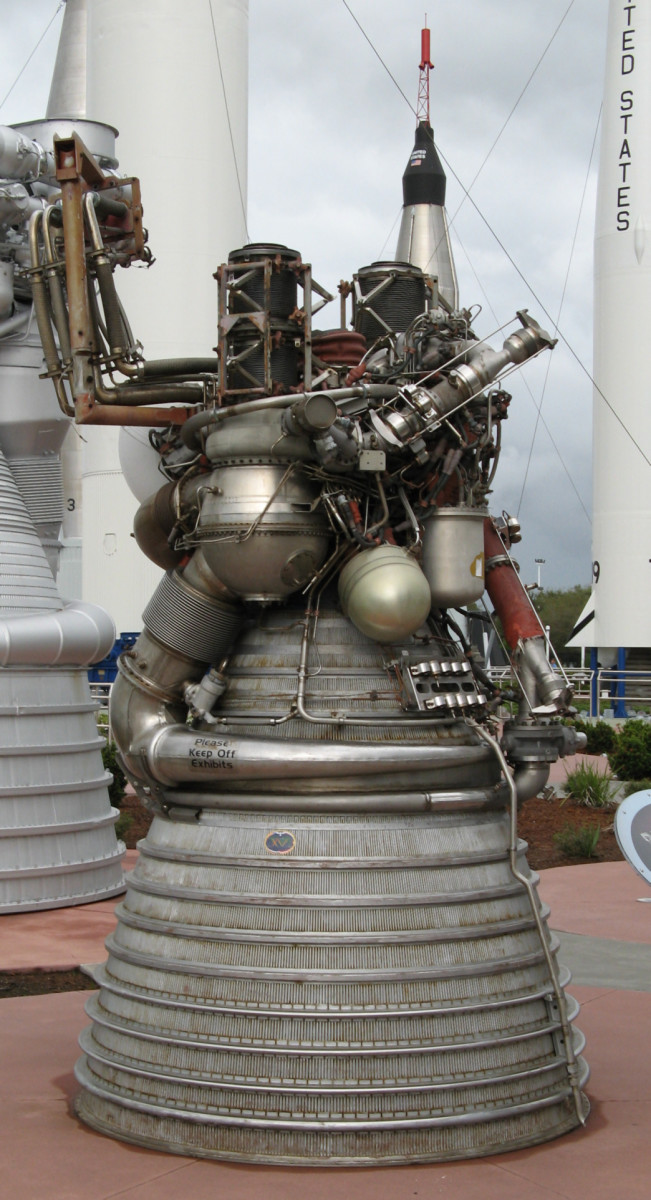
How to Choose A Precision Grinding Vendor
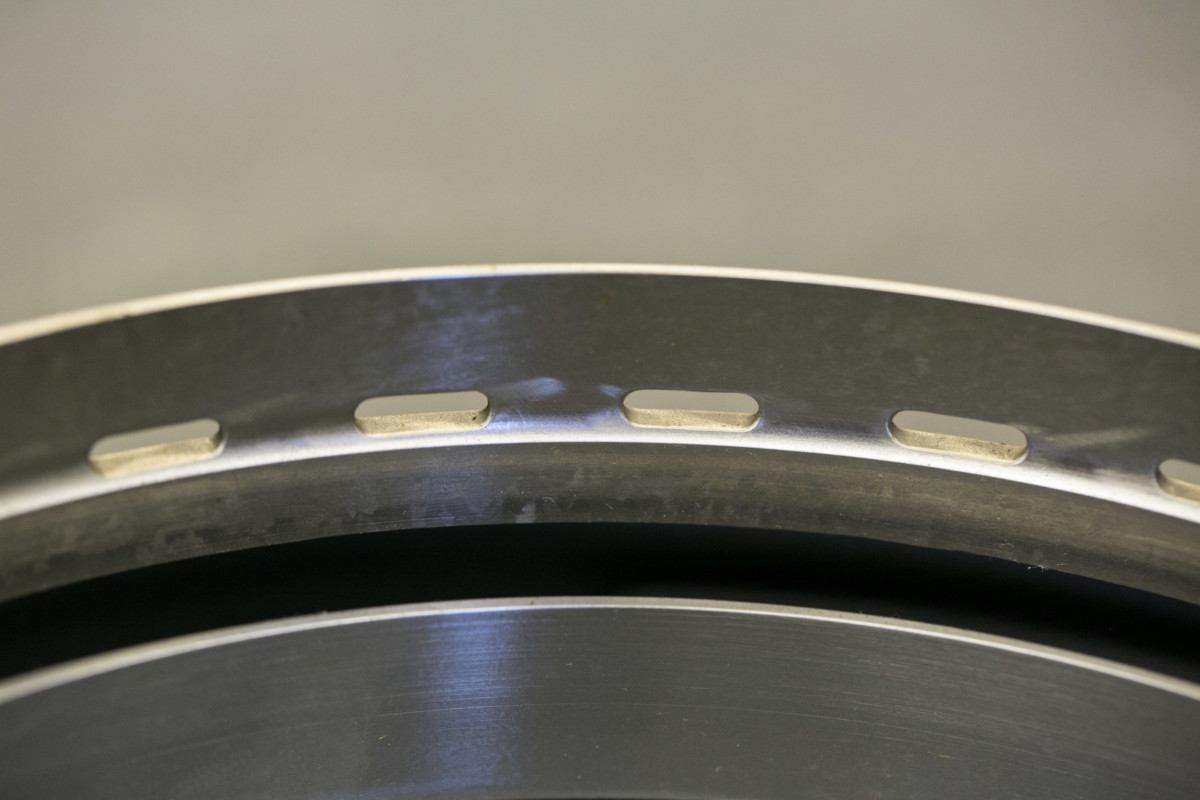